Empower Your Toughest Applications with Our Heavy Duty Hydraulic Cylinders
Built to Last, Perform, and Excel Under Pressure.
HEAVY DUTY HYDRAULIC CYLINDERS
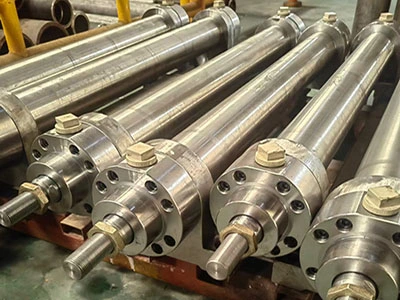
Industrial Powerhouse
Showcasing the robust design of our heavy duty hydraulic cylinder, ideal for rigorous industrial applications.
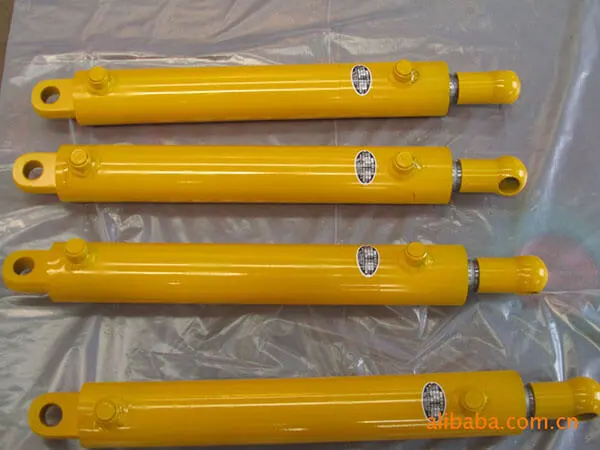
Precision in Action
Precise control and power in a manufacturing setting, highlighting its high-capacity performance.
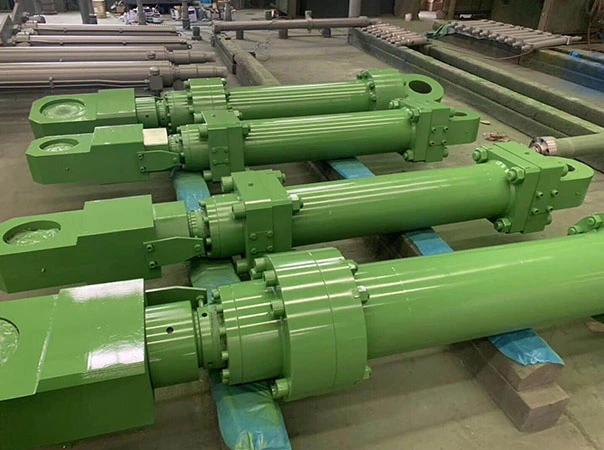
Built to Last
Featuring reinforced construction, designed for durability and longevity under tough conditions.
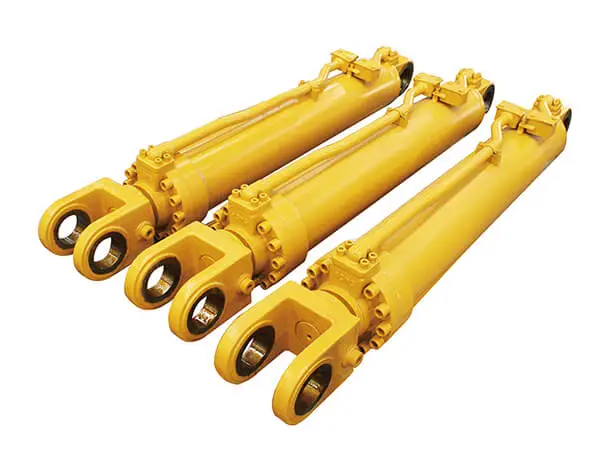
Customized Solution
Custom-engineered to meet specific client needs, this hydraulic cylinder features unique adaptations for specialized applications.
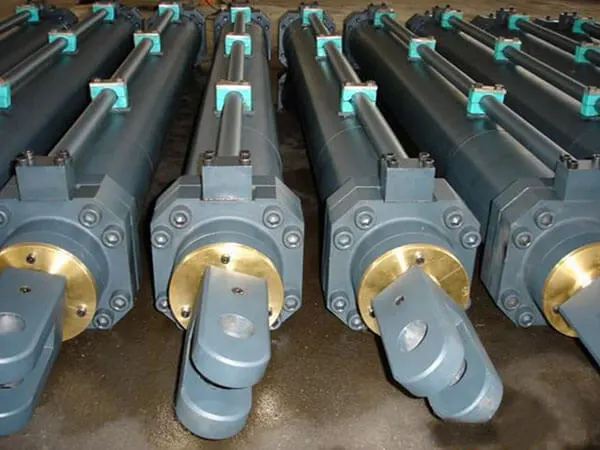
Versatile Performer
Displayed in a construction environment, this cylinder exemplifies versatility across various heavy machinery applications.
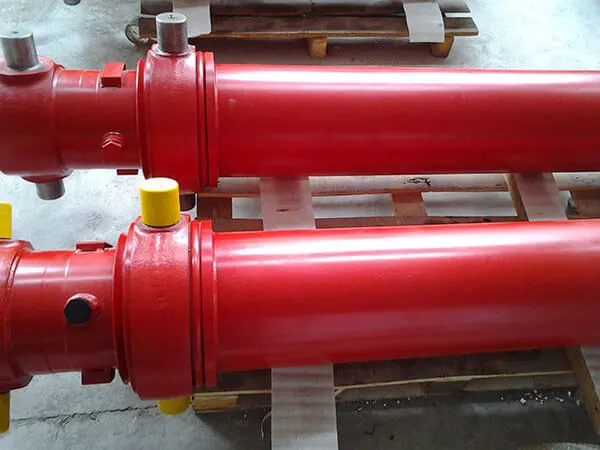
High-Pressure Operation
This model is optimized for high-pressure tasks, ensuring reliable operation and exceptional force output.
Heavy Duty Hydraulic Cylinder Manufacturer
Introduction to Heavy Duty Hydraulic Cylinders
Heavy duty hydraulic cylinders are built tough to handle the toughest jobs in industries like construction, mining, and manufacturing. They’re designed to withstand extreme conditions with reinforced structures and top-quality materials, ensuring they last longer and perform reliably under heavy loads. Perfect for pushing, lifting, or pulling, these cylinders come with hardened steel rods and robust seals to keep them going strong without frequent maintenance.
Our heavy duty cylinders are all about durability and versatility. They’re customizable to fit specific needs, with options for size, stroke length, mounting types, and pressure capacities. Whether you’re lifting heavy materials or operating rugged machinery, these cylinders are engineered to boost efficiency and reduce downtime.
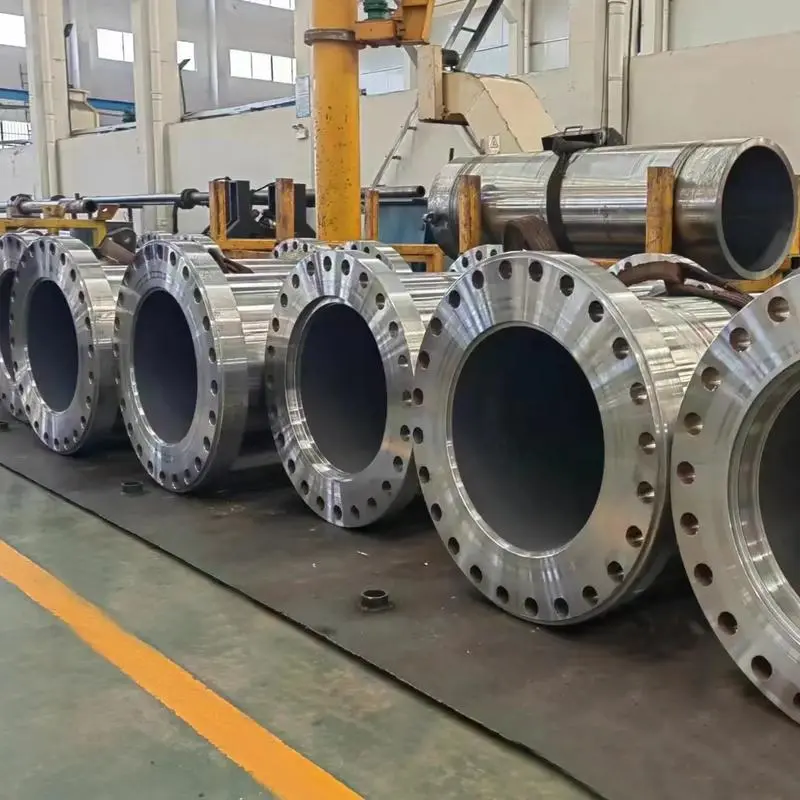
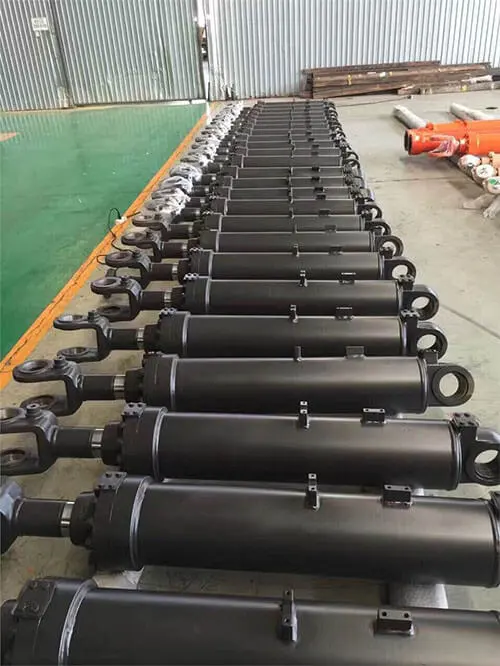
FEATURES & BENEFITS
Enhanced Load Capacity
Designed to handle heavy loads with exceptional stability.
Superior Construction
Crafted from high-strength materials resistant to wear and tear.
Advanced Sealing Technology
Ensures leak-free performance and extended lifecycle.
Maximize Uptime
Reduce maintenance intervals with our robust construction.
Increase Efficiency
High power-to-weight ratio for more effective operations.
Custom Fit
Available in multiple configurations to meet specific industry needs.
TECHNICAL SPECIFICATIONS
Our Heavy Duty Hydraulic Cylinders are meticulously designed to suit a range of industrial demands with the following technical characteristics
Maximum Operating Pressure
Heavy duty hydraulic cylinders are typically designed to handle high pressures, with common ratings up to 3000 psi (pounds per square inch) and, for more extreme applications, even higher.
Stroke Length
These cylinders come in a variety of stroke lengths, from a few inches to several feet, depending on the specific requirements of the application.
Bore Size
The bore size can range from 2 inches to over 24 inches, accommodating the need for different force outputs required by various industrial applications.
Rod Diameter
The diameter of the cylinder rod is crucial for determining the load-bearing capacity. Heavier loads require thicker rods to resist bending and breaking under stress.
Material Composition
Commonly made from high-strength steel, such as 4140 or 4340 alloys, for the cylinder body and rod, providing excellent toughness and resistance to wear and corrosion. Some cylinders also incorporate bronze or specialized composite materials for components like rod guides and seals to enhance performance in harsh environments.
Seal Types
To prevent leaks and maintain efficiency, heavy duty hydraulic cylinders use high-quality seals such as polyurethane, nitrile, or fluorocarbon. Some are designed for low friction and others for high temperature and chemical resistance, depending on the application’s requirements.
Mounting Options
These cylinders offer various mounting options to suit different machinery layouts and operational demands, including flange mounts, clevis mounts, foot mounts, and trunnion mounts. Each type provides different advantages in terms of load-bearing capacity and ease of installation.
Major Components of Heavy Duty Hydraulic Cylinder
Heavy duty hydraulic cylinders are composed of several key components, each crucial to their function and performance. Here are the main parts that make up these robust system
These parts work together to convert hydraulic energy into mechanical energy, allowing heavy duty hydraulic cylinders to perform various lifting, pushing, and pulling tasks in tough industrial settings.
Cylinder Barrel
The main body of the cylinder which houses the piston and the hydraulic fluid. It is typically made from high-strength steel to withstand high pressures and prevent deformation.
Piston
Located inside the cylinder barrel, the piston separates the two hydraulic fluid chambers. It moves back and forth under pressure, creating movement that is transmitted through the piston rod.
Piston Rod
This is the component that extends from the cylinder and connects to the machinery or load being moved. It is usually made from hardened steel to resist bending and wear.
Rod Seal
Prevents hydraulic fluid from leaking past the piston rod when it extends and retracts. This is crucial for maintaining the efficiency and cleanliness of the system.
End Caps
These are fitted to the ends of the cylinder barrel and help contain the hydraulic fluid within. They also serve as mounting points for the cylinder and often contain the rod seal and wiper.
Wiper Seal
Located on the external part of the rod where it exits the cylinder, the wiper seal cleans the rod to prevent contaminants from entering the cylinder, which could cause damage and wear.
Ports
These are the entry and exit points for the hydraulic fluid located on the cylinder body or end caps. The ports connect to hoses or pipes that lead to the hydraulic system’s pump and reservoir.
Bushings and Bearings
These components are often found where the piston rod exits the cylinder and helps to reduce friction and wear on the rod as it moves.
Installation Guide: Detailed Steps for Heavy Duty Hydraulic Cylinders
Pre-Installation Check:
- Verify that all components are intact and undamaged upon arrival.
- Ensure compatibility of the hydraulic cylinder with other system components in terms of size, pressure ratings, and mounting requirements.
Mounting:
- Choose the correct mounting type based on the application’s load and motion requirements (flange, foot, clevis, or trunnion).
- Securely attach the mounting hardware to prevent movement that could lead to misalignment.
- Use torque wrenches to tighten bolts to the manufacturer’s specified torque settings to avoid over-tightening.
Alignment:
- Properly align the cylinder to prevent side loading, which can cause premature wear and failure. Ensure that the cylinder is parallel to the application’s direction of force.
- Use precision tools like levels and laser aligners for accuracy.
Hydraulic Connections:
- Clean all connection points before attaching hoses or pipes to prevent contamination.
- Apply appropriate sealants if necessary to avoid leaks.
- Ensure that hydraulic fluid paths are clear and free of obstructions.
System Check:
- Once installed, slowly pressurize the system to check for any leaks or misalignments.
- Observe the cylinder’s operation to ensure it is functioning smoothly without any unusual noises or movements.
Maintenance Tips: Ensuring Durability and Efficiency
Regular Inspections:
- Conduct scheduled inspections to check for signs of wear, corrosion, or damage, particularly on the piston rod and seals.
- Look for hydraulic fluid leaks around the seals and connection points.
Lubrication:
- Regularly lubricate moving parts such as bearings and joints to reduce friction and wear.
- Use the lubricant recommended by the manufacturer for best results.
Hydraulic Fluid Maintenance:
- Monitor and maintain hydraulic fluid levels and condition. Change the fluid at intervals specified by the manufacturer or based on fluid condition tests.
- Use high-quality fluids suited to your system’s specifications and operating environment to prevent corrosion, contamination, and thermal degradation.
Seal Replacement:
- Replace seals and o-rings at the first sign of wear or leakage to maintain system integrity and prevent contamination.
- Keep spare seals on hand for quick replacement during routine maintenance.
Cleanliness:
- Keep the external parts of the cylinder and the surrounding area clean to prevent dirt or debris from entering the system.
- Regularly clean the piston rod surface to remove any potential contaminants that could breach the seal.
Record Keeping:
- Maintain detailed records of all maintenance activities, inspections, and replacements. This documentation can help identify recurring issues or predict potential failures before they occur.
Start Today!
Send us a message if you have any questions or request a quote. Our experts will give you a reply within 8 hours.
- +86 755 3360 3110
- +86 159 8989 1944
- info@hydroforcecylinders.com